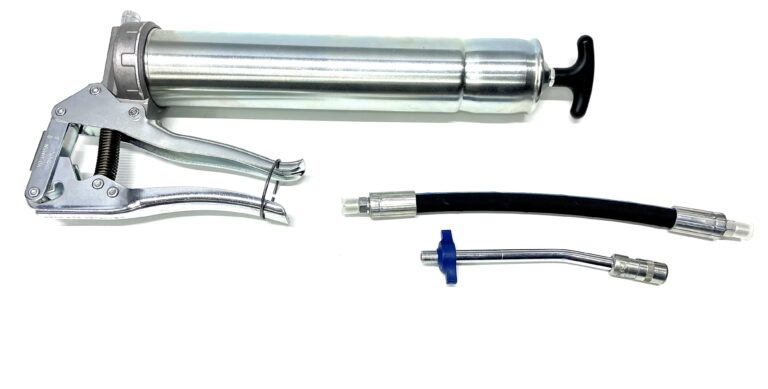
The Importance of Grease Guns
When it comes to slaughterhouse maintenance, ensuring the longevity and efficiency of equipment is very important. One of the most effective tools in achieving this is the humble grease gun.
Despite its simple appearance, the grease gun plays a crucial role in maintaining and extending the life of abattoir equipment. By providing consistent and precise lubrication, grease guns help to reduce wear and tear, prevent breakdowns, and ensure smooth operation of machinery.
Grease Gun Benefits
The benefits of using a grease gun are numerous. Firstly, it allows for the targeted application of lubricant, ensuring that each component receives the right amount of grease.
This precision is vital in high-use environments such as South Africa abattoir care, where machinery is subjected to constant heavy use. Grease guns help to minimise friction between moving parts, reducing the risk of damage and extending the life of the equipment.
Another significant benefit is the reduction of maintenance costs. By regularly lubricating equipment with grease guns, the need for expensive repairs or replacements is diminished.
This cost-saving aspect is particularly important for smaller operations, such as Johannesburg butchery tools, where budgets may be more constrained.
Lubrication Tools and Techniques
Lubrication is a critical aspect of slaughterhouse maintenance. Without proper lubrication, machinery can quickly become inefficient and prone to breakdowns. Grease guns are an essential part of the toolkit, allowing for easy and effective industrial grease application.
There are various types of grease guns, each suited to different tasks and equipment types.
- Manual Grease Guns: These are the most common and versatile. They are operated by hand and provide excellent control over the amount of grease applied.
- Pneumatic Grease Guns: These are powered by compressed air and are ideal for large-scale operations where speed and efficiency are critical.
- Battery-Powered Grease Guns: These offer the convenience of portability and ease of use, making them suitable for maintenance tasks in various locations within an abattoir.
The choice of grease gun depends on the specific needs of the operation and the type of equipment being maintained. Regardless of the type, the key is to ensure regular and thorough lubrication.
Best Practices for Abattoir Equipment Longevity
To maximise the lifespan of abattoir equipment, it is essential to follow best practices for lubrication and maintenance. Regular maintenance schedules should be established, detailing when and how each piece of equipment should be lubricated.
This proactive approach helps to identify potential issues before they become major problems.
- Regular Inspections: Conduct routine inspections to check for signs of wear and tear. Early detection of issues can prevent costly repairs and downtime.
- Proper Lubricant Selection: Use the right type of grease for each piece of equipment. Different components may require specific lubricants to perform optimally.
- Consistent Application: Ensure that grease is applied consistently and thoroughly. Grease guns are designed to deliver precise amounts, so take advantage of this feature to cover all necessary areas.
The Role of Grease Guns in Industrial Settings
In industrial settings such as South Africa abattoir care, grease guns are indispensable tools. The harsh conditions and constant use of equipment necessitate regular lubrication to maintain performance. By using grease guns, operators can ensure that machinery runs smoothly, reducing the risk of unexpected breakdowns and extending the equipment’s overall lifespan.
Impact on Operational Efficiency
The use of grease guns directly impacts the operational efficiency of a slaughterhouse. Proper lubrication helps to maintain the functionality of equipment, allowing for uninterrupted workflow.
This efficiency is crucial in high-demand environments like Johannesburg meat processing facilities, where any downtime can have significant financial implications.
Environmental Considerations
While maintaining equipment is essential, it’s also important to consider the environmental impact of lubrication practices. Using grease guns allows for precise application, minimising waste and reducing the risk of environmental contamination.
Selecting environmentally friendly lubricants and following best practices for disposal can further enhance the sustainability of slaughterhouse maintenance practices.
The Origins of Grease Guns
The invention of the grease gun dates back to the early 20th century. It is widely attributed to a desire to simplify and improve the lubrication process of machinery.
Early industrialisation brought about the need for a more efficient way to maintain equipment, leading to the development of tools that could precisely apply lubricants to moving parts.
The grease gun was born out of this necessity, providing a practical solution for consistent and controlled lubrication.
Widespread Use in the Meat Industry
The adoption of grease guns in the meat industry, particularly within abattoirs and slaughterhouses, began to gain traction in the mid-20th century. As the meat processing industry grew and operations became more mechanised, the need for regular and effective maintenance of machinery became critical.
The grease gun offered a straightforward and reliable method for applying grease to essential components, thereby enhancing the longevity and performance of slaughterhouse equipment.
In the 1950s and 1960s, grease guns became standard equipment in abattoirs. Their use ensured that machines operated smoothly, reducing downtime and maintenance costs.
The ability to apply grease precisely and efficiently made the grease gun an indispensable tool in these high-demand environments. This period marked the beginning of widespread reliance on grease guns for maintaining abattoir equipment.
Advancements and Modern Innovations
Since their initial development, grease guns have undergone significant advancements, leading to the modern, efficient tools used today in slaughterhouse maintenance.
- Manual to Pneumatic: The transition from manual grease guns to pneumatic (air-powered) models was a significant advancement. Pneumatic grease guns allowed for faster and more consistent application of grease, which was especially beneficial in large-scale operations such as South Africa abattoir care. These models reduced the physical effort required by operators and increased the efficiency of lubrication tasks.
- Battery-Powered Innovations: The introduction of battery-powered grease guns brought a new level of convenience and portability. These tools combined the precision of manual grease guns with the efficiency of pneumatic models, making them ideal for various settings, from large abattoirs to smaller butcheries. Battery-powered grease guns are particularly useful in environments like Johannesburg meat processing, where mobility and ease of use are essential.
- Smart Technology: Modern grease guns now incorporate smart technology features, such as digital meters and automated grease delivery systems. These innovations ensure that the correct amount of grease is applied consistently, reducing waste and further enhancing abattoir equipment longevity. The integration of smart technology also allows for better tracking and monitoring of lubrication schedules, ensuring that maintenance tasks are performed regularly and efficiently.
- Eco-Friendly Lubricants: Advances in lubricant technology have also impacted the use of grease guns. Environmentally friendly greases are now available, reducing the environmental impact of industrial lubrication practices. This development is particularly significant in regions like South Africa, where sustainability is a growing concern.
The Role of Grease Guns Today
Today, grease guns remain a cornerstone of slaughterhouse maintenance. Their ability to provide precise and controlled lubrication is crucial for maintaining the efficiency and longevity of abattoir equipment.
In high-use environments such as Johannesburg butchery tools settings, grease guns help to ensure that machinery operates smoothly and safely, reducing the risk of breakdowns and extending the life of critical components.
By continuously evolving and incorporating new technologies, grease guns have maintained their relevance and importance in the meat processing industry. Whether through manual, pneumatic, or battery-powered models, these tools remain essential for effective industrial grease application.
OVERVIEW
The grease gun has come a long way since its early 20th-century origins. From its widespread adoption in the mid-20th century to the modern advancements seen today, the grease gun continues to play a vital role in maintaining the efficiency and longevity of abattoir equipment. As the meat processing industry evolves, so too will the tools and techniques used to ensure its success.
SUMMARY
The role of grease guns in extending the life of abattoir equipment cannot be overstated. The benefits of precise industrial grease application are clear, from reducing maintenance costs to ensuring operational efficiency. By following best practices for abattoir saw blade care and using the right lubrication tools, facilities can enhance the longevity and performance of their machinery.
Whether in large industrial settings or smaller butcheries, grease guns are an indispensable part of slaughterhouse maintenance, contributing to the overall success and sustainability of the meat processing industry in South Africa and beyond.