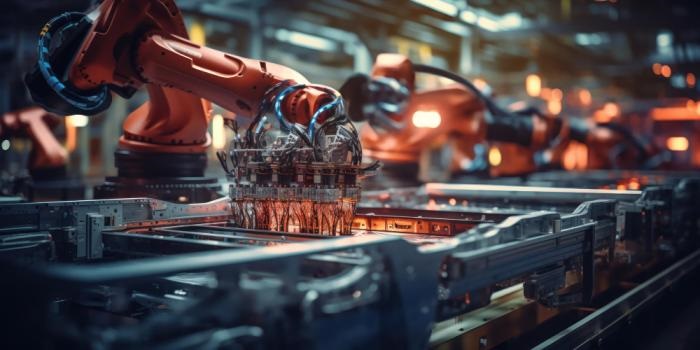
Introduction
Industry 4.0, also known as the Fourth Industrial Revolution, signifies a transformative shift in the manufacturing sector, driven by advancements in digital technologies. This paradigm encompasses cyber-physical systems, the Internet of Things (IoT), cloud computing, and artificial intelligence (AI), which collectively revolutionize traditional manufacturing and enterprise resource planning (ERP) systems. In this article, we will explore how Industry 4.0 impacts manufacturing software development and manufacturing ERP system development, detailing the profound changes, opportunities, and challenges brought by this revolution.
The Evolution of Industry 4.0
Historical Context
Industry 4.0 follows the previous industrial revolutions, each marked by significant technological advancements. The first industrial revolution was characterized by mechanization and steam power, the second by mass production and electricity, and the third by automation and computers. Industry 4.0 builds on these foundations, introducing smart and autonomous systems fueled by data and machine learning.
Key Technologies
- Cyber-Physical Systems (CPS): Integration of physical processes with digital systems, enabling real-time data collection and analysis.
- Internet of Things (IoT): Network of interconnected devices that communicate and exchange data, enhancing operational efficiency.
- Cloud Computing: Provides scalable computing resources and storage, facilitating data access and collaboration.
- Artificial Intelligence (AI) and Machine Learning (ML): Algorithms that enable machines to learn from data, predict outcomes, and make decisions.
- Big Data and Analytics: Massive datasets analyzed to uncover patterns, trends, and insights that drive informed decision-making.
- Additive Manufacturing: Technologies like 3D printing that allow for precise, customized production.
Impact on Manufacturing Software Development
Enhanced Connectivity and Integration
Industry 4.0 promotes seamless connectivity between devices and systems, leading to integrated manufacturing environments. Manufacturing software development must now prioritize interoperability, ensuring that disparate systems and devices can communicate effectively. This integration allows for real-time data exchange, which is crucial for optimizing production processes.
- Interoperability Standards: Developing software that adheres to interoperability standards like OPC UA (Open Platform Communications Unified Architecture) ensures compatibility across various devices and systems.
- API Development: Creating robust APIs (Application Programming Interfaces) to facilitate communication between software platforms, machines, and sensors.
Real-Time Data and Analytics
The ability to collect and analyze data in real-time is a cornerstone of Industry 4.0. Manufacturing software development now focuses on creating platforms that can handle vast amounts of data and provide actionable insights.
- Data Acquisition and Management: Developing software capable of acquiring data from various sources, such as sensors, machines, and ERP systems, and managing this data efficiently.
- Advanced Analytics Tools: Integrating advanced analytics tools that use AI and ML to process data, predict maintenance needs, optimize production schedules, and improve quality control.
Predictive Maintenance and Asset Management
Predictive maintenance is a significant advancement brought by Industry 4.0, reducing downtime and extending equipment life. Manufacturing software development incorporates predictive maintenance algorithms and asset management features.
- Condition Monitoring: Software that continuously monitors the condition of machinery and equipment, using data from IoT devices to predict failures before they occur.
- Maintenance Scheduling: Developing intelligent scheduling systems that plan maintenance activities during non-peak times, minimizing production disruption.
Customization and Flexibility
Industry 4.0 enables mass customization, allowing manufacturers to produce personalized products efficiently. Manufacturing software development must support flexible production systems that can quickly adapt to changing customer demands.
- Flexible Manufacturing Systems (FMS): Software that supports FMS, enabling quick reconfiguration of production lines for different products.
- Order Management: Enhancing order management systems to handle customized orders, track production progress, and ensure timely delivery.
Impact on Manufacturing ERP System Development
Integration of Advanced Technologies
Manufacturing ERP system development now integrates advanced technologies like IoT, AI, and cloud computing to enhance functionality and performance.
- IoT Integration: Embedding IoT capabilities within ERP systems to provide real-time visibility into production processes, inventory levels, and supply chain activities.
- AI and ML Integration: Leveraging AI and ML to automate decision-making processes, optimize resource allocation, and improve demand forecasting.
- Cloud-Based ERP Solutions: Developing cloud-based ERP solutions that offer scalability, accessibility, and reduced IT infrastructure costs.
Enhanced Data Management and Analytics
Modern ERP systems are designed to handle large volumes of data generated by connected devices and systems. The focus is on data integration, management, and analytics.
- Data Integration: Ensuring seamless data integration from various sources, including shop floor machines, sensors, and external partners.
- Advanced Analytics: Incorporating advanced analytics capabilities to provide insights into production efficiency, supply chain performance, and financial health.
Improved Supply Chain Management
Industry 4.0 enhances supply chain visibility and coordination. ERP systems now include advanced supply chain management features that leverage real-time data.
- Supply Chain Visibility: Developing features that provide real-time visibility into the entire supply chain, from raw material procurement to product delivery.
- Supply Chain Coordination: Using AI to optimize supply chain operations, such as demand forecasting, inventory management, and logistics planning.
User Experience and Mobility
Modern ERP systems prioritize user experience and mobility, allowing users to access critical information and perform tasks from anywhere.
- User-Friendly Interfaces: Designing intuitive interfaces that simplify complex processes and enhance user productivity.
- Mobile ERP Applications: Developing mobile applications that enable users to access ERP functionalities on the go, improving responsiveness and decision-making.
Opportunities and Challenges
Opportunities
- Increased Efficiency: Industry 4.0 technologies streamline manufacturing processes, reducing waste and improving efficiency.
- Enhanced Agility: Manufacturers can quickly adapt to market changes and customer demands, offering personalized products and services.
- Data-Driven Decision Making: Real-time data and advanced analytics enable informed decision-making, leading to better outcomes.
- Competitive Advantage: Early adopters of Industry 4.0 technologies can gain a significant competitive edge in the market.
Challenges
- Complexity and Integration: Integrating diverse technologies and systems can be complex and require significant resources.
- Data Security: With increased connectivity comes heightened risk of cyberattacks, necessitating robust cybersecurity measures.
- Skills Gap: Implementing Industry 4.0 technologies requires a workforce with advanced technical skills, which may be in short supply.
- Cost: The initial investment in Industry 4.0 technologies can be substantial, posing a barrier for small and medium-sized enterprises (SMEs).
Case Studies
Siemens
Siemens is a leader in implementing Industry 4.0 technologies. The company’s Digital Enterprise Suite integrates IoT, AI, and cloud computing into their manufacturing processes, enhancing efficiency and flexibility.
- Digital Twin: Siemens uses digital twin technology to create virtual replicas of physical assets, enabling real-time monitoring and predictive maintenance.
- MindSphere: Siemens’ cloud-based IoT operating system, MindSphere, connects products, plants, systems, and machines, facilitating data analysis and decision-making.
General Electric (GE)
General Electric has embraced Industry 4.0 through its Brilliant Manufacturing Suite, which incorporates advanced analytics, IoT, and AI.
- Predix Platform: GE’s Predix platform is an industrial IoT solution that collects and analyzes data from machines, helping optimize performance and reduce downtime.
- Proficy Software: GE’s Proficy software suite provides tools for real-time data analysis, predictive maintenance, and production optimization.
Bosch
Bosch utilizes Industry 4.0 technologies to improve manufacturing efficiency and product quality.
- Bosch Production System (BPS): BPS integrates IoT and AI to monitor production processes, identify inefficiencies, and implement corrective actions.
- Nexeed Software: Bosch’s Nexeed software solution provides real-time data on production, logistics, and quality, enhancing overall operational efficiency.
Future Trends
Advanced Robotics and Automation
The future of manufacturing will see increased use of advanced robotics and automation. Robots equipped with AI will perform complex tasks, enhancing productivity and reducing human error.
- Collaborative Robots (Cobots): Cobots work alongside human operators, increasing efficiency and safety on the shop floor.
- Autonomous Mobile Robots (AMRs): AMRs navigate manufacturing environments independently, transporting materials and products.
Edge Computing
Edge computing will become more prevalent, processing data closer to the source rather than relying on centralized cloud servers. This approach reduces latency and enhances real-time decision-making.
- Local Data Processing: Edge devices process data locally, enabling faster responses to critical events.
- Enhanced Security: Edge computing reduces the amount of data transmitted over networks, minimizing cybersecurity risks.
Blockchain Technology
Blockchain technology will improve transparency and security in manufacturing and supply chain processes. Immutable ledgers will ensure data integrity and traceability.
- Supply Chain Traceability: Blockchain provides a transparent record of product movement through the supply chain, enhancing trust and accountability.
- Smart Contracts: Automated, self-executing contracts on blockchain platforms streamline transactions and reduce administrative overhead.
Conclusion
Industry 4.0 represents a transformative shift in manufacturing, driven by digital technologies that enhance connectivity, data analysis, and automation. The impact on manufacturing software development and manufacturing ERP system development is profound, with new opportunities for efficiency, customization, and data-driven decision-making. However, challenges such as complexity, cybersecurity, and skills gaps must be addressed to fully realize the potential of Industry 4.0. As manufacturers continue to adopt and integrate these technologies, the future of manufacturing promises to be more agile, efficient, and innovative.